Hot Products
This reduces maintenance costs for wood shredders
With the popularity of wood shredding machine in all walks of life, our wood deep processing industry has entered a stage of rapid development. But many customers in the acquisition of wood shredding machine, do not pay attention to the daily maintenance of wood shredding machine, until the equipment is faulty or other problems, will think of solving, do not know the prevention gradually. So we need to remind our customers that the crusher is assembled by metal parts, metal will present chemical reactions such as rust and so on, so the usual protection is also very important.
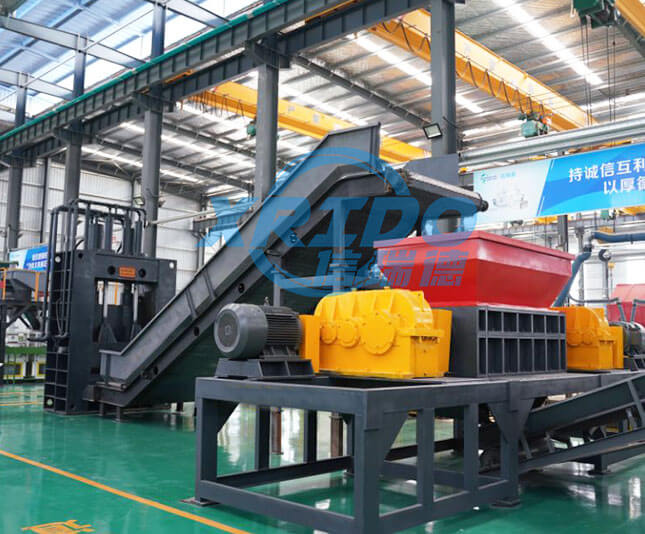
So what are the main parts of the daily maintenance of the wood shredding machine? For example: Transmission parts lubrication, crusher internal cleaning and a little reinforcement of fixed bolts, these are the daily need to maintain, so in the face of customers on how to maintain and protect the wood shredding machine to reduce production costs, especially the wood shredding machine in the use of the process of maintenance and protection and later wear parts for a simple answer, Ensuring that there are no problems during use can also reduce maintenance costs on the other hand.
1. Check whether all parts of the machine are installed in place before operation. If there is any loosening of the screws and bolts, tighten them immediately. Pull the belt gently to test the rotation. If there is any collision with the shell, see whether the rotation direction of the machine is correct.
2, the machine before running let it idling for a few minutes, found that there is no abnormal sound, and then start to evenly blanking, to ensure the normal operation of the machine, it is prohibited to overload the motor, to ensure the normal operation of the machine.
3. In addition to checking whether various parts are loose, the daily inspection work should also check the wear condition of wearing parts. We should timely replace the new wearing parts found to be seriously worn to ensure the normal operation of the equipment.
4. Fill the bearing with butter regularly. Good lubricity is also conducive to increasing output and increasing the service life of equipment. Under normal circumstances, the bearing temperature is not more than 70°. When the bearing temperature is found to be too high in the work, it should be stopped immediately for inspection, to find out the reason, and to continue to put into production after troubleshooting.